Foundry Industry 4 Point O
Early one morning, I looked up the Industrial Revolution 4.0, and my first attempt at reading about it was a jumble of new jargon and buzzwords that I couldn’t deal with before coffee. The pundits currently say we’re on the Fourth industrial revolution. Pre-caffinated cogerism aside, industrial revolutions have been fairly important to the manufacturing sector, so I dug down into the cereal box and pulled out the magic decoder ring. The following is a look at the tangible elements of this next wave of technology cresting over the foundry industry, and how it is starting to impact the shop floor.
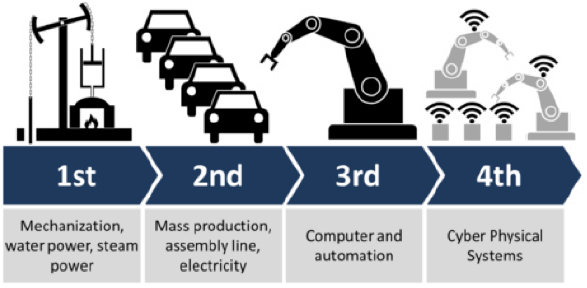
1From Wikipedia https://en.wikipedia.org/wiki/Industry_4.0
In the First Industrial Revolution we stopped making everything by hand, and started tooling up machines to make things faster, cheaper, and more consistently. People still did most all of the work and made all the decisions. In the Second Industrial Revolution we set up our tools in assembly lines, used electricity and simple, physical automation to make more stuff, faster, cheaper, with less thought, and less people. In the Third Industrial Revolution we used computers, digital data, and motorized systems to streamline the design, production, and quality control of production, and started to log data – but people were still ultimately in charge of and required for all decisions that required thinking.
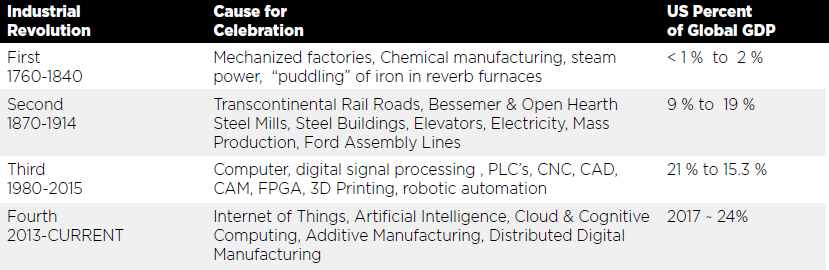
The WORLD GDP HAS RISEN FROM < $1.5 Trillion in 1960 to > $75 Trillion in 2016
As we enter the Fourth Industrial Revolution we are mechanizing the thinking process. We can use wearable devices to monitor worker body temperature and stress levels to help prevent injuries. Adaptive machine learning can eliminate worker learning curves. Factories can monitor stock levels and order raw materials based on market prices and customer purchase orders. Production lines can perform tool changes in advance of scrap being produced and schedule maintenance on themselves prior to the occurrence of system failures. All of this possible due to artificial intelligence that can make decentralized decisions – i.e computers that can analyze data and execute plans without human intervention.
INDUSTRIAL REVOLUTION 4.0: CORE PRINCIPLES OF SMART FACTORIES
Cyber-Physical Systems
Modular "smart" equipment & devices that monitor physical processes & make decentralized decisions without human interaction required – or to augment the capability of human operators.
Internet Of Things
Digital devices with internet connectivity that can communicate and cooperate with each other and with humans in real time. Includes sensors (know what is happening) and actuators (make things happen). An evolution of data logging and PLCs.
Cloud Computing
(Connectivity) – Accessible over internet, massively powered shared computing resources and compilations of data that far exceed the capabilities of any one company. Only possible through global economy of scale of computing resources.
Cognitive Computing
Artificial intelligence that encompasses adaptive machine learning, natural language processing, speech recognition, vision recognition, emotion analysis and biometric scanning, enabling true human-computer interaction and dialog. Systems like IBM’s Watson can make independent contextual decisions based on large sets of unstructured data. New advanced AI is capable reasoning of iterative problem solving from incomplete or ambiguous data, such as weather, video, physical senses.
So what will the Fifth Industrial Revolution be? The groundwork has already started. So far, all the marketing, apps, tools, and products have been "seller driven". Companies, entrepreneurs, engineers and designers decide what to make, based on what they think that you want – and then they sell it to you. My crystal ball says that the 5th Industrial Revolution will grow from the automation of individual buyers' agents – when the mechanization of the creative process allows the consumer to pull what they want or need from the economy on demand.